HVAC systems form the backbone of environmental comfort in modern structures, from residential buildings to commercial premises. They control temperature, regulate humidity, and ensure proper ventilation, thereby creating a comfortable and healthy indoor environment.
In this intricate network of components, sheet metal is a common sight in HVAC systems. But it doesn’t exist merely as a structural element; it plays a pivotal role in the overall functioning and efficiency of these systems.
This article delves into the topic of HVAC sheet metal fabrication, offering insights into the process, its importance, and how Monster Builder, a leading metal works company, excels in this domain.
HVAC Sheet Metal Fabrication: Commonly Used Materials
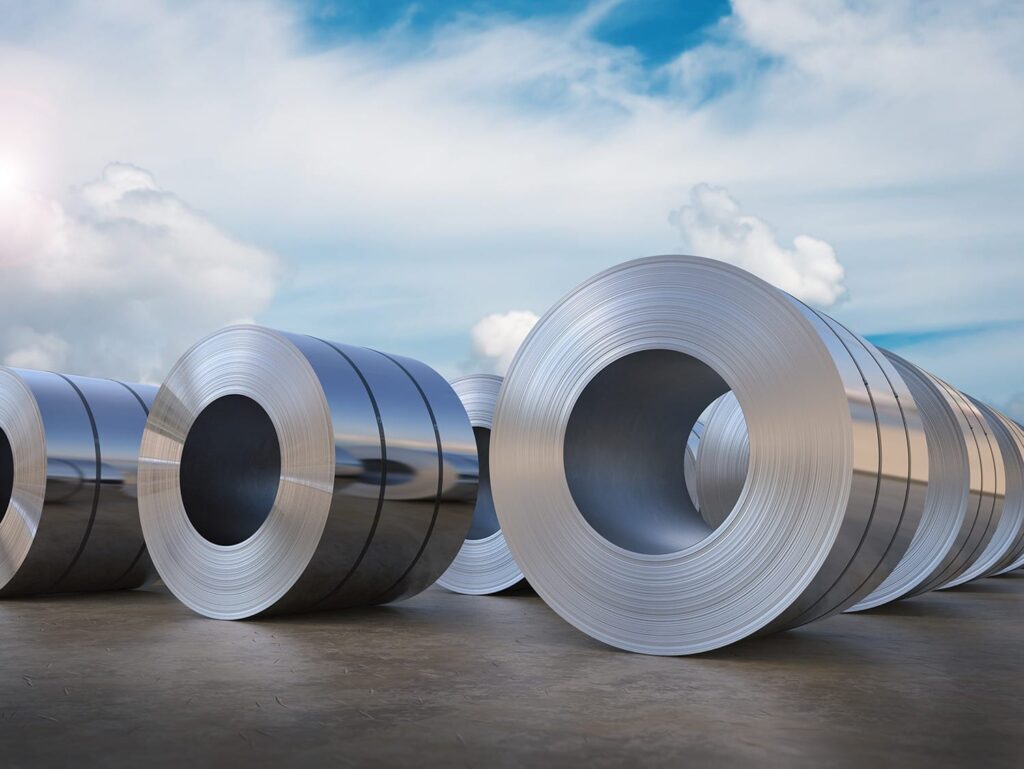
When it comes to HVAC systems, the choice of material used for sheet metal fabrication is crucial as it directly impacts the system’s efficiency, longevity, and overall performance.
While a vast array of materials might be available for sheet metal fabrication, not all are suitable for use within HVAC systems. Specific metals are chosen based on their unique properties that make them ideal for this application.
In this section, we’ll discuss some of the most commonly used materials in sheet metal fabrication for HVAC systems, and explain the unique properties that make them suitable for such applications.
1. Aluminum
Aluminum is a popular choice for HVAC sheet metal fabrication due to its lightweight nature, which makes it easier to work with and install.
Despite being lightweight, aluminum is tough, resistant to corrosion, and has excellent thermal conductivity, making it ideal for heat exchange applications within HVAC systems.
Additionally, aluminum is highly recyclable, aligning with the growing push towards sustainability in many industries, further cementing its position as a favored material in HVAC systems.
2. Galvanized Steel
Galvanized steel is steel that has been coated with a protective layer of zinc to prevent rusting and corrosion.
This material is known for its strength and durability, making it an excellent choice for the ductwork in HVAC systems that require a robust and long-lasting material.
Galvanized steel’s ability to resist moisture also makes it suitable for use in HVAC systems where condensation can be a concern.
3. Stainless Steel
Stainless steel, a variant of steel that contains chromium, brings to the table unparalleled resistance to corrosion and rust. This characteristic makes it an ideal candidate for HVAC systems, especially those exposed to high-humidity or corrosive environments.
Furthermore, the strength and durability of stainless steel enable it to withstand intense pressure and temperature fluctuations, making it a versatile choice for a myriad of HVAC applications.
4. Copper
Copper finds significant use in HVAC systems, especially in heat exchangers, refrigerant lines, and coils. This is primarily due to its superior thermal conductivity, which allows for rapid and efficient heat transfer.
Its resistance to corrosion further enhances its desirability in HVAC systems. Additionally, copper’s antimicrobial properties can help improve indoor air quality by mitigating the risk of bacterial and fungal proliferation within the HVAC system.
Applications of Sheet Metal Fabrication in HVAC Systems
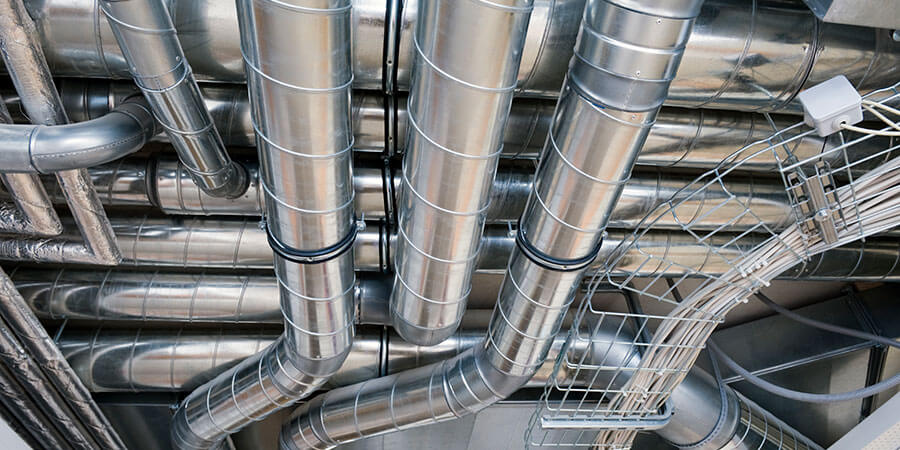
The HVAC industry’s reliance on sheet metal cannot be overstated. As a versatile and durable material, sheet metal plays a pivotal role in the construction and operation of HVAC systems.
Applications of sheet metal span an array of components, including ductwork, coils, roof curbs, and refrigerant lines. This section offers a detailed exploration of these applications, demonstrating the breadth and scope of sheet metal’s contribution to HVAC technology.
1. Ductwork: The Veins of an HVAC System
Perhaps the most visible and well-known application of sheet metal in HVAC systems is in the fabrication of ductwork. Acting as the circulatory system of an HVAC unit, ductwork carries conditioned air from the system and distributes it throughout the building.
Given its critical role, ductwork must be robust and efficient, providing a seamless pathway for air to travel. Sheet metal, with its strength and durability, is the material of choice for this purpose.
With its resistance to rust and corrosion, galvanized steel is commonly used to construct ductwork. The metal is formed into rectangular or cylindrical shapes to create the ducts, with the size and layout of the ductwork customized based on the building’s size and design.
2. Coils: The Heart of Heat Transfer
Another critical application of sheet metal in HVAC systems is found in the coils. These components are the heart of the heating and cooling process, facilitating the transfer of heat to condition the air.
Copper is often the metal of choice for these coils due to its excellent thermal conductivity. Copper coils, surrounded by aluminum fins, allow for effective heat exchange, a critical factor in the HVAC system’s performance.
3. Roof Curbs: The Sturdy Support
Roof curbs, used to support rooftop HVAC units, are another component often constructed of sheet metal. These structures need to withstand the weight of the HVAC unit, resist the elements, and last for the lifetime of the system.
Galvanized steel, known for its strength and longevity, is often used to fabricate roof curbs. The sheet metal is formed to match the footprint of the HVAC unit, providing a secure and durable platform for the system to rest upon.
4. Refrigerant Lines: The Pathway for Cooling
Refrigerant lines, which carry the refrigerant between the indoor and outdoor units of an HVAC system, are also often made of sheet metal. These lines must be strong and leak-proof, ensuring that the refrigerant can move freely and efficiently through the system.
When it comes to sheet metal fabrication for HVAC, copper is the preferred material for refrigerant lines. It is chosen for its combination of strength, thermal conductivity, and corrosion resistance.
Summary: Common Types of Sheet Metal Used in HVAC and Their Properties
Sheet Metal Type | Strength | Corrosion Resistance | Thermal Conductivity | Common Use |
---|---|---|---|---|
Aluminum | Medium | Medium | High | Ductwork, coils |
Galvanized Steel | High | High | Low | Ductwork, roof curbs |
Stainless Steel | High | High | Low | Specialized components |
Copper | High | Medium | High | Coils, refrigerant lines |
The Process of Sheet Metal Fabrication for HVAC
HVAC sheet metal fabrication is a complex, multi-stage process that transforms a flat piece of metal into a fully functional component of an HVAC system.
This process combines a deep understanding of material science, advanced machinery, and skilled craftsmanship. What follows is a detailed exploration of the steps involved in the HVAC sheet metal fabrication process, presented in a manner that remains accessible to both industry professionals and laypersons alike.
Step 1: Designing the Component
The first phase in the fabrication process is to design the HVAC component. This step involves using Computer-Aided Design (CAD) software to create a precise digital blueprint of the component.
The design phase is critical as it dictates the dimensions, shape, and specifications of the final product. The CAD software allows for precise measurements and complex designs, ensuring that the fabricated piece will fit perfectly within the HVAC system.
Step 2: Selecting the Material
Upon completion of the design phase, an appropriate sheet metal type is selected based on the requirements of the specific HVAC component.
As discussed in the previous sections, materials like aluminum, steel, and copper are commonly used in HVAC systems. Each material offers unique advantages, such as corrosion resistance, strength, conductivity, or weight, which must be carefully considered to select the best metal for the job.
Step 3: Cutting and Forming the Metal
The selected sheet metal is then cut into the required shape using either laser cutting, plasma cutting, or water jet cutting. These high-precision cutting methods allow for intricate designs to be cut with remarkable accuracy, ensuring that the component aligns with the specifications outlined in the design phase.
Once cut, the metal is formed into the desired shape. This step involves bending, folding, or rolling the metal using a variety of machinery. The specific processes used will depend on the complexity of the component and the properties of the chosen metal.
Step 4: Assembling the Component
The next phase in the fabrication process is the assembly of the cut and formed pieces. This might involve welding, riveting, or using adhesives to join the parts together.
The assembly stage requires a great deal of precision to ensure that the final product aligns with the design specifications and fits seamlessly within the HVAC system.
Step 5: Finishing the Component
The final step in the HVAC metal fabrication fabrication process is finishing the component. This could involve sanding to smooth any rough edges, applying a protective coating to enhance corrosion resistance, or painting the component to match the aesthetics of the HVAC system.
The finishing process not only improves the appearance of the component but also enhances its durability and lifespan. For example, galvanized steel is often coated with a layer of zinc to improve its resistance to rust and corrosion.
Summary: Steps in the HVAC Sheet Metal Fabrication Process
Step | Description |
---|---|
1. Design | Creating a digital blueprint of the component using CAD software. |
2. Material Selection | Choosing the appropriate sheet metal based on the component requirements. |
3. Cutting & Forming | Cutting the metal into the required shape and then forming it. |
4. Assembly | Joining the cut and formed pieces together. |
5. Finishing | Smoothing rough edges, applying protective coating, or painting the component. |
Advantages of Sheet Metal Fabrication for HVAC
The use of sheet metal fabrication in HVAC systems is not by happenstance.
This method offers a plethora of benefits that make it a preferred choice in the industry. From customizability to sustainability, sheet metal fabrication brings a sundry of advantages that bolster HVAC systems’ efficiency, durability, and overall performance.
The following section delves into these benefits, painting a comprehensive picture of why sheet metal fabrication is indispensable in the HVAC industry.
1. Customizability and Precision
In the world of HVAC, one size doesn’t fit all. Every building presents unique challenges and requirements, necessitating a high degree of customizability.
Sheet metal fabrication shines in this aspect, allowing for the creation of HVAC components tailored to specific dimensions and shapes.
Advanced techniques such as Computer-Aided Design (CAD) and Computer-Aided Manufacturing (CAM), for example, enable precision in the creation of components, ensuring they fit perfectly into the intended space, enhancing the system’s overall efficiency.
2. Cost-Effectiveness
Sheet metal fabrication is also an economically viable choice for building HVAC systems as the process allows for the efficient use of materials, minimizing waste and thus reducing costs.
Additionally, the long lifespan and durability of sheet metals like galvanized steel and stainless steel mean fewer replacement costs over the system’s lifetime.
Furthermore, the lightweight nature of materials such as aluminum can simplify and reduce the cost of installation and transportation.
3. Durability and Strength
When it comes to strength and durability, sheet metal stands tall. Materials like galvanized steel and stainless steel are known for their robustness, capable of withstanding rigorous conditions while maintaining their integrity.
This characteristic makes them ideal for components like ductwork and roof curbs, which need to be resilient and long-lasting.
Moreover, the corrosion-resistant nature of these metals extends the life of HVAC components, contributing to a system that lasts longer and performs consistently.
4. Lightweight and Flexibility
Despite their strength, many sheet metals used in HVAC systems are surprisingly lightweight.
Aluminum, for example, is known for its excellent strength-to-weight ratio. This lightness offers several advantages, including easier handling and installation and less structural support required in the case of rooftop units.
Sheet metal is also malleable, allowing it to be bent, folded, and shaped into a variety of forms, adding to its versatility in HVAC applications.
5. Efficiency and Performance
Sheet metal fabrication also contributes to the efficiency and performance of HVAC systems.
With the ability to create airtight and leak-free ductwork, the energy efficiency of the HVAC system is significantly improved.
Furthermore, the excellent thermal conductivity of materials like copper used in coils and refrigerant lines enhances heat transfer efficiency, leading to better system performance.
6. Easy Maintenance and Repairs
Sheet metal components are typically easier to maintain and repair. Their robustness reduces the frequency of necessary repairs, and when maintenance is required, sheet metal parts can often be cleaned, patched, or replaced with relative ease.
This accessibility contributes to the longevity of the HVAC system and aids in maintaining its optimal performance over time.
7. Sustainability: Towards a Greener Future
Last but not least, sheet metal fabrication aligns with sustainability goals. Metals like aluminum and steel are recyclable, making sheet metal components a more environmentally friendly choice.
Additionally, the improved energy efficiency of HVAC systems utilizing sheet metal components contributes to lower energy consumption, aligning with green building standards and reducing the carbon footprint.
Summary: Advantages of Sheet Metal Fabrication for HVAC
Advantage | Description |
---|---|
Customizability & Precision | Ability to create HVAC components tailored to specific dimensions and shapes. |
Cost-Effective | Efficient use of materials, minimizing waste and reducing costs. |
Durability & Strength | Ability to withstand rigorous conditions while maintaining integrity. |
Lightweight & Flexible | Easier handling and installation, and less structural support required. |
Efficiency & Performance | Creation of airtight and leak-free ductwork, improving system efficiency. |
Maintenance & Repairs | Easier to maintain and repair, contributing to system longevity. |
Sustainability | Aligns with sustainability goals, as metals used are recyclable and improve energy efficiency. |
Importance of Quality in HVAC Sheet Metal Fabrication
Quality control in HVAC sheet metal fabrication is of paramount importance. High-quality sheet metal components contribute to the overall efficiency, durability, and cost-effectiveness of HVAC systems.
Well-fabricated sheet metal ductwork, for example, ensures an airtight passage for conditioned air, preventing leakages that could lead to energy loss and increased utility bills.
Moreover, high-quality sheet metal is resistant to common issues like rust and corrosion, ensuring that the HVAC system remains robust and functional for a longer time.
Monster Builder: Your Trusted Provider of HVAC Sheet Metal Fabrication
At Monster Builder, we take pride in delivering top-notch HVAC sheet metal fabrication services. Our experienced team, coupled with state-of-the-art machinery, produces high-quality sheet metal components that meet the exacting standards of the HVAC industry.
We follow a rigorous quality control process that scrutinizes every stage of fabrication, from design to finishing. Our commitment to craftsmanship ensures that every piece we produce is precise, robust, and fit for purpose.
Furthermore, our advanced CNC machines allow us to achieve a high level of accuracy and consistency, ensuring that every product meets the required specifications and standards.
Whether you’re an HVAC contractor seeking reliable sheet metal components or a building owner looking to upgrade your HVAC system, we’re here to help. Feel free to contact us today and explore how our expertise in HVAC sheet metal fabrication can serve your needs.
Monster Builder: Your Trusted Metal Works Specialist
Monster Builder is a premier provider of sheet metal fabrication, CNC machining, 3D Printing, and rapid prototyping services.
With advanced technology, competitive pricing, rapid turnaround, and global shipping capabilities, Monster Builder can be trusted for your next project.