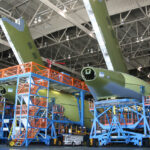
Menu
Vacuum casting, also known as vacuum-assisted casting or polyurethane vacuum casting, is a rapid prototyping and low-volume production method used to create high-quality replicas of prototypes or small-scale production parts. It’s particularly well-suited for producing functional prototypes, limited production runs, or components with intricate geometries.
Vacuum casting, a pivotal player in the realm of rapid prototyping, empowers your vision to materialize with unparalleled accuracy. Through a meticulous process, we replicate intricate details and complex geometries, ensuring your prototypes mirror the final product’s characteristics. Our cutting-edge vacuum casting technology creates multiple high-quality replicas from a master pattern, making it an ideal choice for testing, validation, and market research.
However, it’s important to note that vacuum casting might have limitations such as size constraints, limited material choices, and potential surface imperfections. The success of the process depends on the quality of the master model, the expertise of the operator, and the suitability of the casting material for the intended application. Below are some limitations of vacuum casting:
At Monster Builder, our team of seasoned professionals is committed to harnessing the full potential of your projects, with a strong emphasis on quality, innovation, and your satisfaction. We leverage advanced technology and deep industry knowledge to deliver high-quality parts that meet your precise specifications. Reach out to us today to explore how our vacuum casting services can elevate your production needs.
Quality Services
rapid turnaround
advanced Technology
Yes, we would be happy to provide a quote for your project. Please contact us using the “GET A QUOTE” form, WhatsApp us at (+65) 87743624, email us at contact@monsterbuilder.ai or the Live Chat on our website.
Yes, we have the capability to handle both small and large volume orders. Our advanced equipment and experienced team allow us to efficiently produce high-quality parts and components in large quantities.
Our typical fabrication lead time is 8 calendar days.
Yes! We ship our products globally.
All available materials can be viewed on our materials page. If you have any questions or need further assistance, please don’t hesitate to get in touch.
Our Location
Singapore Headquarters:
15 Little Rd, #04-02, Singapore 536988
Quick Links