In the world of metal works, particularly when dealing with aluminum, the choice of metal finishing can significantly impact a product’s lifespan, performance, and aesthetics.
Two of the most common aluminum finishing methods are anodizing and powder coating. Straddling the intersection of science and art, these processes enhance aluminum’s natural resilience and beauty, making it a preferred material for various applications.
In this article, we will provide a comprehensive comparison between anodizing vs powder coating, shedding light on their pros, cons, and best-use scenarios.
What is Anodizing?
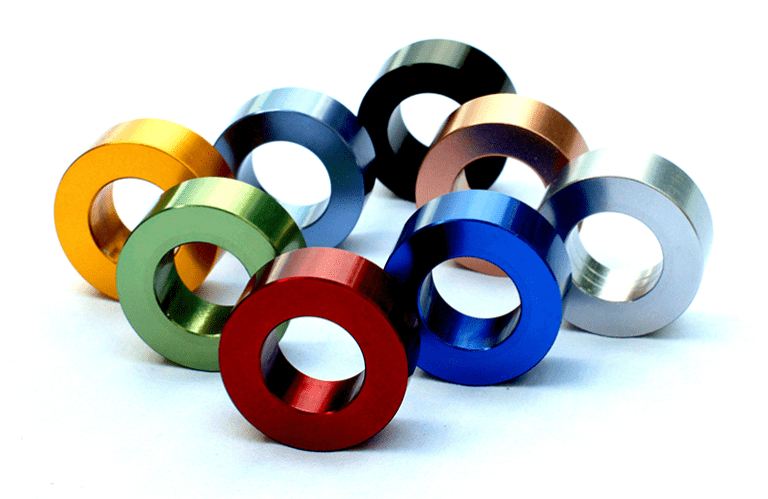
Anodizing, a common aluminum finishing method, is an electrochemical process that boosts the natural oxide layer on the surface of aluminum. But what exactly does this mean? To understand this, we must first delve into the properties of aluminum and the nature of its oxide layer.
Aluminum, like other metals, naturally reacts with oxygen in the environment. This reaction forms a thin layer of aluminum oxide on the surface of the metal. This oxide layer is hard and resistant to corrosion, acting as a protective shield for the underlying aluminum. This is why aluminum does not rust like iron and steel.
However, the natural oxide layer on aluminum is typically thin, often less than a micrometer thick. While it offers a certain degree of protection, this layer can be made even more robust and durable through the process of anodizing. This is where the science of electrochemistry comes into play.
In the anodizing process, the aluminum piece is submerged in an electrolytic solution, typically a weak sulfuric acid bath. The aluminum acts as the anode (the positively charged electrode), hence the term ‘anodizing’. A cathode, typically a plate of lead or stainless steel, is also submerged in the bath.
When an electric current is passed through the solution, oxygen ions are formed at the aluminum surface. These ions react with the aluminum to create a thicker, harder layer of aluminum oxide. This artificially enhanced oxide layer can be up to 100 times thicker than the natural oxide layer, providing much greater protection against corrosion and wear.
The anodizing process also creates a porous surface on the aluminum. This porosity can be beneficial as it allows for the absorption of dyes for coloring the aluminum, or for the application of lubricants in moving parts. The final step in the anodizing process is sealing, which closes these pores to further increase the corrosion resistance and prevent dirt ingress.
Advantages of Anodizing
One of the primary benefits of anodizing is the enhanced durability it imparts. The anodizing process culminates in the formation of an aluminum oxide layer on the surface of the part. This layer is integrated with the underlying aluminum substrate, resulting in a hard, wear-resistant surface that significantly improves corrosion resistance. This aspect of anodizing makes it an excellent choice for parts that will be exposed to harsh environments or demanding usage conditions.
As the anodizing process can be manipulated to create a range of attractive finishes, anodizing also has the advantage of enhancing the aesthetic qualities of aluminum parts. These include various colors, such as black, gold, or clear, and a range of textures, such as glossy and matte. This versatility makes anodizing a popular choice in industries where both function and form are important, such as consumer electronics and architecture.
Disadvantages of Anodizing
While anodizing can produce a range of attractive finishes, achieving certain colors can be challenging. In the anodizing process, colors are created by dyeing the porous oxide layer. However, not all dyes are equally effective or stable, and some colors, particularly bright and vibrant ones, can be difficult to achieve. Furthermore, color consistency can be hard to maintain across different batches, which can be a concern in applications where color matching is crucial.
Another limitation of anodizing is that it’s a complex process that requires careful control of numerous variables, including temperature, voltage, and the acidity of the electrolyte bath. Mistakes in any of these areas can lead to suboptimal results, such as an uneven finish or inadequate thickness of the oxide layer. This complexity can increase the cost of anodizing, particularly for smaller production runs.
What is Powder Coating?
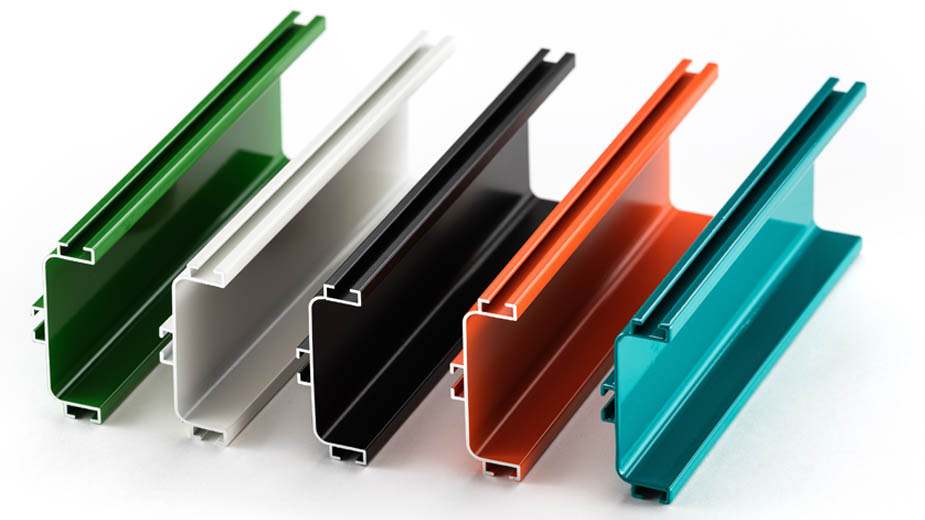
Powder coating is a finishing process that employs the use of a dry coating material. It has a stark contrast to other finishing methods, such as traditional liquid painting or electroplating, which use wet or liquid applications.
The powder used in this process is a blend of finely ground particles of resin and pigment, which together form a ‘powder’. This powder is electrostatically charged and sprayed onto the surface of the object that is to be coated. This electrostatic charge causes the powder particles to be attracted to the surface, adhering to it much like iron filings to a magnet.
Once the object has been coated with the powder, it is then placed in a curing oven. The high temperatures of the oven cause the powder to melt, flowing across the surface of the object to form a smooth and continuous coating. As the coating cools, it hardens into a durable and attractive finish.
Advantages of Powder Coating
Powder coating offers its own unique set of advantages. One of the most significant benefits is its minimal environmental impact. Unlike liquid coatings, powder coatings emit zero or near zero volatile organic compounds (VOCs). Any unused or overspray powder can also be recycled, making it an environmentally friendly option.
Apart from environmental friendliness, powder coating also offers an expansive spectrum of aesthetic possibilities. It can be formulated to create a myriad of colors, textures, and finishes, such as high-gloss, matte, metallic, and clear. This versatility allows builders to achieve the desired appearance for a product.
Disadvantages of Powder Coating
Despite the various benefits of powder coating as a metal finishing option, achieving thin finishes with powder coating can be challenging. This is because the nature of the powder coating process tends to produce thicker coatings compared to conventional liquid paints. While this characteristic is beneficial for durability, it can be a disadvantage for components that require thin yet robust coatings.
Additionally, the curing process of powder coating requires a high-temperature oven to melt and fuse the powder onto the metal surface. This necessity for heat can be a disadvantage when dealing with heat-sensitive materials or components. Components that may warp or deform at high temperatures are not suitable candidates for powder coating.
Furthermore, applying multiple colors to a single piece can be complex and time-consuming. With powder coating, each color must be applied and cured separately, which can increase the process time and cost. Thus, for designs requiring multiple colors on the same piece, powder coating may not be the most efficient method.
Anodizing vs Powder Coating: How They Compare
Now that we’ve looked at anodizing and powder coating individually, let’s delve into a more in-depth comparison to better understand the powder coat vs anodized debate. We’ll compare these processes based on several criteria, including process, durability and performance, appearance, cost, and environmental impact.
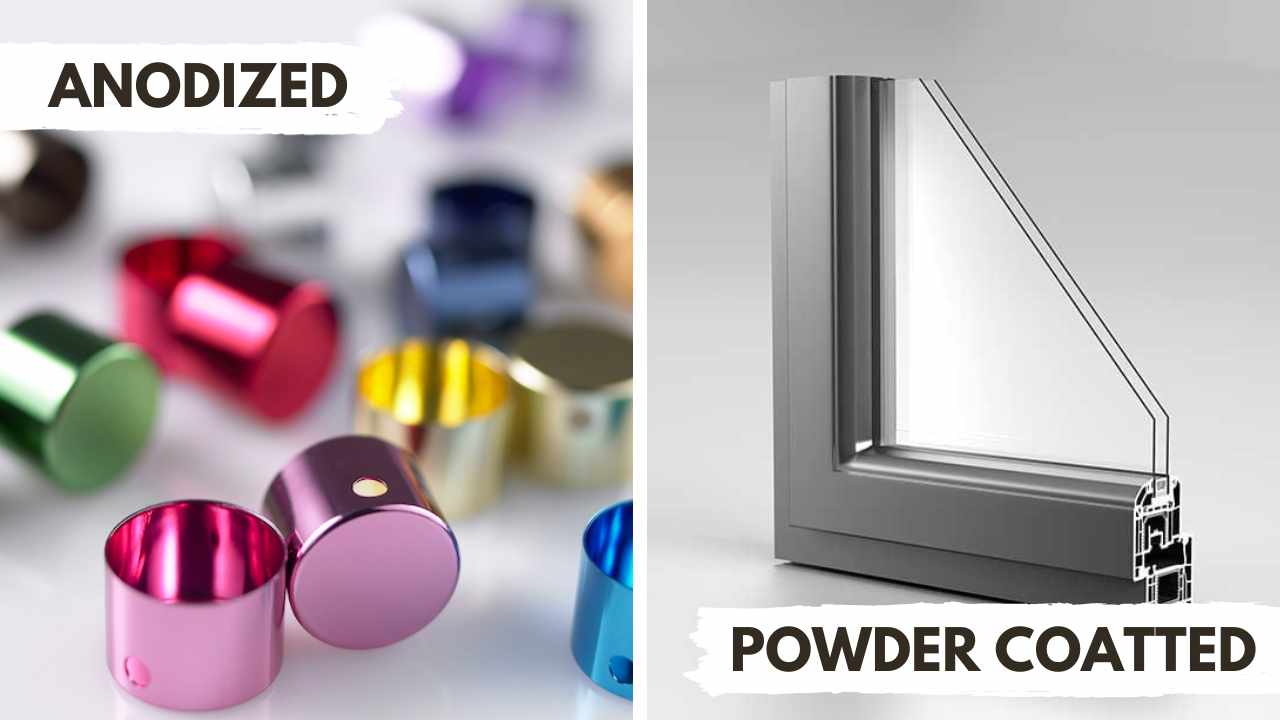
1. Anodized vs Powder Coated: Comparison by Process
Anodizing involves a series of steps: pre-treatment (cleaning and etching), anodizing, coloring (if desired), and sealing. The process requires precise control over variables like temperature and acidity, making it somewhat complex. However, it doesn’t require a curing process, unlike powder coating.
Powder coating, while also requiring pre-treatment, involves a simpler process of applying the coating and curing it in an oven. However, the need for a curing process can be a limitation for large or heat-sensitive parts.
2. Powder Coat vs Anodized: Comparison by Durability and Performance
Both anodizing and powder coating enhance the durability of aluminum parts. Anodizing improves corrosion resistance and wear resistance, whereas powder coating provides a thick, durable finish that’s resistant to chipping and scratching. However, powder coating can be susceptible to UV degradation over time, while anodized finishes maintain their appearance longer.
3. Anodized vs Powder Coat: Comparison by Appearance
In terms of appearance, anodizing preserves the metallic look of aluminum and offers a range of color options if dyed. However, the color range is less extensive than that of powder coating, and the finish can be slightly uneven.
Powder coating offers a wider color range, as well as different textures and patterns that will suit your aesthetic needs. The finish is smooth and even, making it an ideal choice for decorative applications. However, it doesn’t maintain the metallic look of the aluminum.
4. Powder Coating vs Anodizing: Comparison by Cost
Cost is always a crucial factor in manufacturing decisions. In general, the cost for both anodizing and powder coating can vary widely, depending on factors such as part complexity, color choice, and production volume. However, powder coating tends to be more cost-efficient for large batch sizes due to its faster process time and the ability to recycle overspray.
5. Anodizing vs Powder Coating: Comparison by Environmental Impact
In terms of environmental impact, both anodizing and powder coating processes have their advantages. Anodizing uses less energy than powder coating but produces more waste. However, the waste is primarily aluminum hydroxide, which can be recycled or used in other industrial applications.
Powder coating, on the other hand, emits zero or near zero VOCs and allows for powder recycling. However, it requires more energy due to the curing process.
Monster Builder: Your Trusted Metal Works Specialist
Monster Builder is a premier provider of sheet metal fabrication, CNC machining, 3D Printing, and rapid prototyping services.
With advanced technology, competitive pricing, rapid turnaround, and global shipping capabilities, Monster Builder can be trusted for your next project.
Comparison Table: Anodizing vs Powder Coating
Powder coating and anodizing are two popular finishing methods for aluminum, each having their respective benefits and drawbacks.
To make it easier for you to compare the two processes, here’s a comparison table summarizing the key differences between anodizing and powder coating:
Criteria | Anodizing | Powder Coating |
---|---|---|
Process | More complex, no curing required | Simpler, requires curing |
Durability | Excellent corrosion and wear resistance | Thick, durable, chip-resistant |
Appearance | Metallic look, limited color range, slightly uneven finish | Wide color range, smooth finish, non-metallic |
Cost | Varies, generally more suitable for small batches | Varies, generally more cost-effective for large batches |
Environmental Impact | Less energy, more waste (recyclable) | More energy, zero VOCs, recyclable powder |
Common Applications of Anodizing and Powder Coating
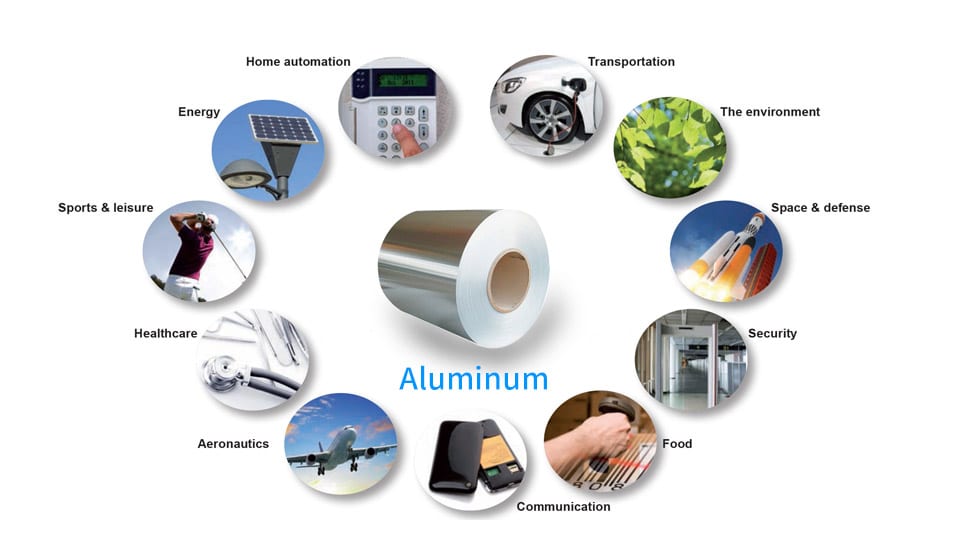
The versatility of both anodized and powder coated aluminum allows for their wide application across numerous industries, each offering unique benefits tailored to specific needs.
Anodizing, beloved for its excellent corrosion resistance, plays a vital role in the aerospace industry, safeguarding aluminum components against the rigors of flight and space travel. Transcending its industrial use, anodizing also lends a weather-resistant, aesthetically pleasing finish to architectural elements like window frames and doors. Even in the realm of electronics, anodized aluminum is a trusted ally, bestowing durability and a sleek appearance on consumer devices such as smartphones and laptops.
Meanwhile, powder coating has carved out its niche in many sectors. Automotive parts like wheels and bumpers sport powder-coated finishes for enhanced durability and custom aesthetics. The outdoor environment poses no threat to powder-coated furniture and appliances, thanks to their UV and weather resistance. Even the fitness industry and industrial manufacturing sectors have embraced powder coating, applying it to gym equipment and machinery for a finish that’s as robust as it is attractive.
Here’s a summary table of the applications of powder coated vs anodized aluminum:
Application Areas | Anodizing | Powder Coating |
---|---|---|
Aerospace | Extensively Used | Less Common |
Architecture | Widely Used | Common |
Electronics | Widely Used | Less Common |
Automotive | Less Common | Extensively Used |
Fitness Equipment | Less Common | Widely Used |
Industrial Machinery | Less Common | Extensively Used |
When to Choose Powder Coating vs Anodizing
The choice between anodizing and powder coating largely depends on the specific application and desired outcome. If you’re looking for a finishing option that enhances corrosion resistance, maintains the metallic look of aluminum, and doesn’t require a smooth, even finish, anodizing would be the better choice.
On the other hand, if you’re aiming for a decorative finish with a wide range of color options, and the parts can withstand the heat of the curing process, powder coating would be your better pick.
Some Last Words
Both anodizing and powder coating offer distinct advantages and potential drawbacks. The choice between getting the finished part anodized or powder coated will ultimately depend on your project’s unique requirements. Whether you’re looking for superior corrosion resistance, a specific aesthetic appeal, or environmentally friendly processes, understanding these two finishing methods can help you make an informed choice.
Here at Monster Builder, we are committed to providing top-notch fabrication and machining services. With our expertise, we can help guide you through the decision-making process to ensure you choose the finish that best suits your needs. Talk to our experts today to discuss your project requirements and see how we can help!
Monster Builder: Your Trusted Metal Works Specialist
Monster Builder is a premier provider of sheet metal fabrication, CNC machining, 3D Printing, and rapid prototyping services.
With advanced technology, competitive pricing, rapid turnaround, and global shipping capabilities, Monster Builder can be trusted for your next project.
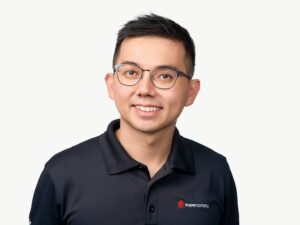
Niles, a seasoned entrepreneur, is the founder of a robotics and automation company. He leads a team of highly skilled engineers, each with decades of experience in mechanical, electrical, and software control. Niles is committed to consistently pushing the boundaries of technology and is dedicated to revolutionizing operational efficiency through the implementation of cutting-edge solutions.